Charcoal, a familiar natural fuel source, extends beyond mere economic value, finding diverse applications from cooking to steel production. Yet, few realize the intricate process behind charcoal production, spanning from raw material selection to the carbonization process.
In this article, we delve into the charcoal production process, exploring raw material choices, key carbonization methods, and modern techniques that enhance production efficiency.
Introduction of Charcoal Production Process
Coming to our Charcoal Production Process, unlike other factories, PNP has a total of 11 steps and each step plays an important role in the production process. To have the best coal quality, PNP always has supervision for each step as well as products are filtered to remove damaged products.
During the charcoal production stages, PNP workshop employees always need to have high concentration and an efficient working regime to achieve the best performance. Besides, to avoid risks during the work process, PNP always checks equipment and furnaces carefully before starting work.
For more detail, below are the detailed steps in the production process that you may find useful :
Step 1 – Cut Wood into Appropriate Size
In the first step of the Charcoal Production Process, the raw material, typically wood, is meticulously cut into the standard size (Length: 90-95cm, Pi: 5-20cm) This initial stage sets the foundation for the entire production process, as the size and uniformity of the wood pieces directly impact the quality and efficiency of the charcoal production.
Precision is key here, as the wood must be cut to dimensions that optimize the carbonization process, ensuring thorough and consistent conversion into charcoal. Additionally, attention is paid to factors such as moisture content and wood species selection, further enhancing the quality of the final product.
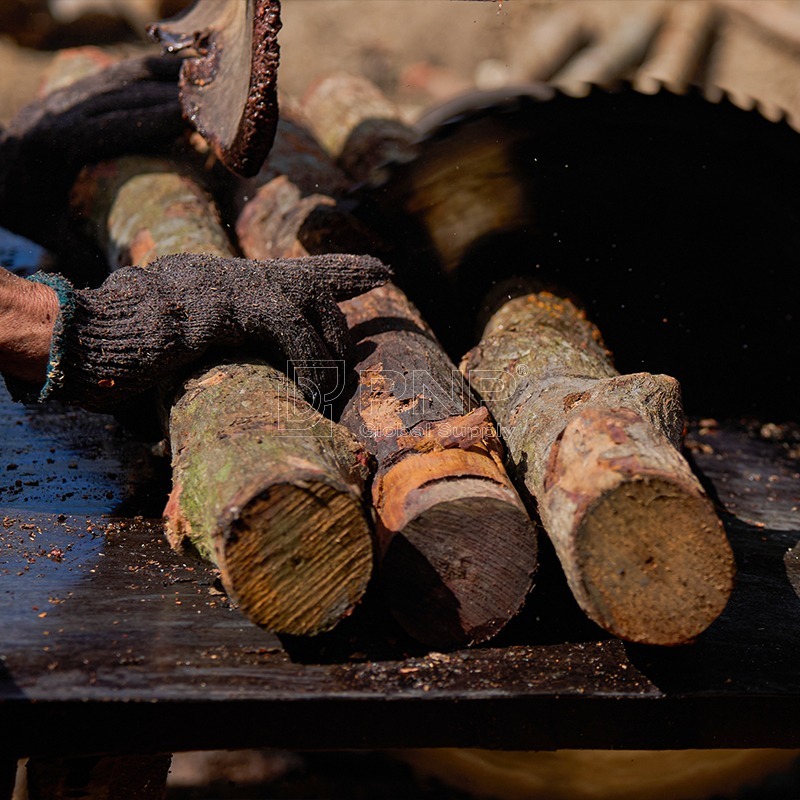
Step 2 – Arranging wood into the kiln
Come with the second step, it’s basic but it’s also important because of the next quality batch . Its preparing the kiln:
- Clean the kiln thoroughly to remove any debris, ash, or leftover charcoal from previous batches. This ensures a clean environment for the new batch of wood.
- Check the ventilation system of the kiln to ensure proper airflow during the carbonization process. Good ventilation helps in even heating and efficient conversion of wood into charcoal.
Then PNP prepares wood for charcoal production, it’s essential to select top-notch hardwoods like oak, maple, or hickory. These types of wood are favored for their dense composition and rich carbon content. Ensuring uniformity, cut the wood into pieces of consistent size. This step promotes even carbonization throughout the wood and maintains a steady level of charcoal quality.
Next step involves arranging the wood for charcoal production. Begin by placing the wood at the bottom of the kiln, establishing a sturdy base. Arrange the pieces either in a crisscross pattern or stack them circularly, allowing for efficient airflow. Continue layering the wood, alternating the grain direction to prevent collapsing and encourage airflow. Leave slight gaps between the pieces to facilitate airflow within the kiln. It’s important not to tightly pack the wood, as this could impede the carbonization process.
When stacking wood, incorporate ventilation holes by intermittently inserting small sticks or rods vertically within the woodpile. These channels facilitate the efficient release of gasses generated during carbonization. It’s crucial to distribute these ventilation holes evenly throughout the stack to uphold uniform heat distribution.
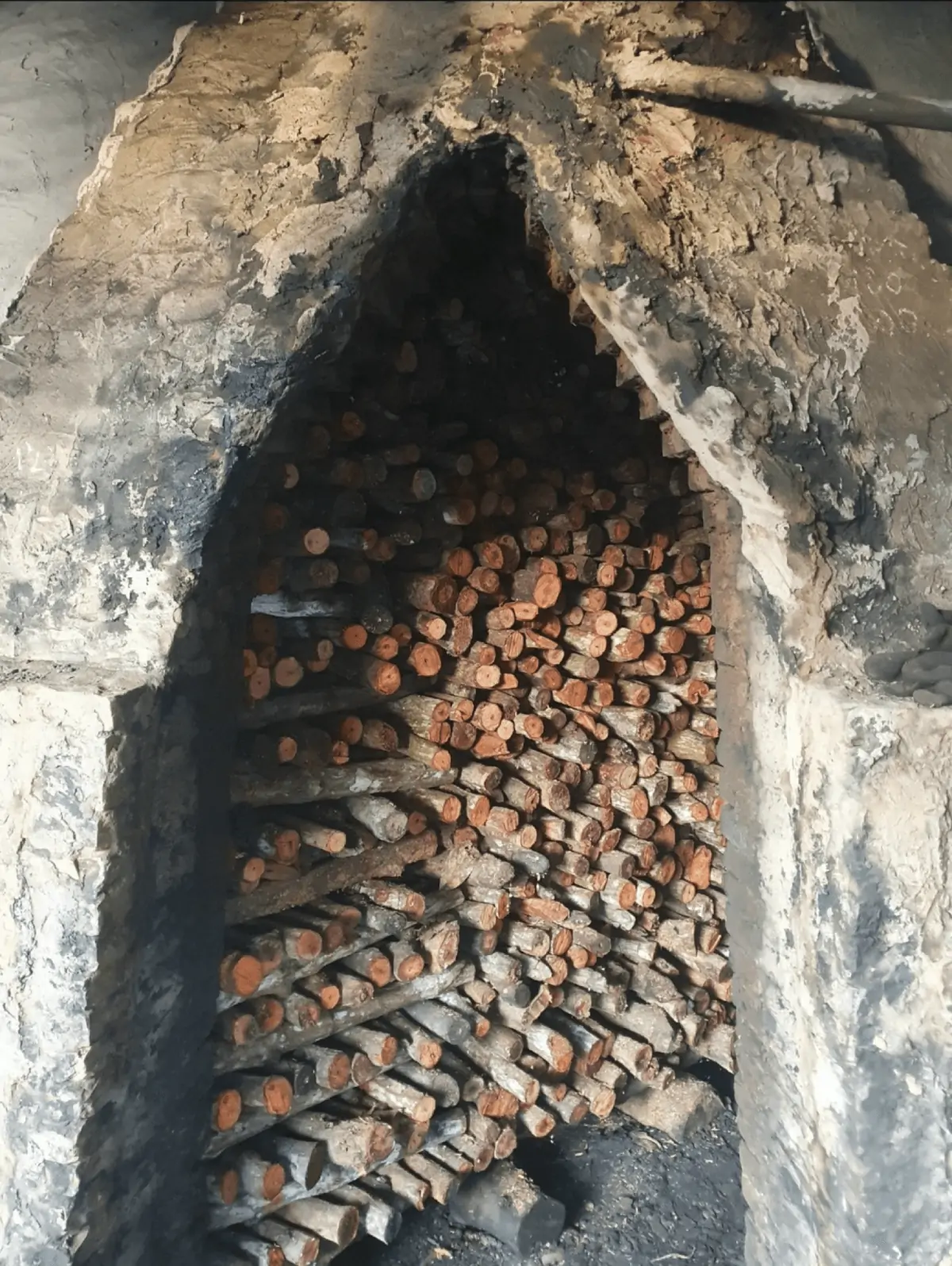
Step 3 – Carbonization Process
To fire up the kiln, begin by lighting a small fire at its base. Slowly increase the intensity of the heat to elevate the temperature inside the kiln. Keep a close eye on the temperature using thermometers or temperature probes. The goal is to sustain a steady temperature throughout the kiln to achieve uniform carbonization of the wood.
After arranging the wood inside the kiln, proceed to cover the top with either leaves, grass, or airtight materials like metal sheets. This covering serves to retain heat within the kiln and limit oxygen access, thereby aiding in the carbonization process. Ensure to seal any gaps or openings around the edges of the kiln cover to prevent air from entering during carbonization.
This process is gonna happen in about 15 – 20 days and the condition is burning the wood according to the carbon conversion process (Temperature > 450C).
Step 4 – Cooling and Charcoal Removal
After the carbonization process finishes, let the kiln cool down slowly. Refrain from opening the kiln too soon, as sudden oxygen exposure might lead to charcoal ignition. Once the kiln reaches a safe temperature, cautiously remove the cover and take out the charcoal. Handle the charcoal delicately to prevent any damage or contamination.
Following removal, the charcoal is allowed to cool further outside the kiln to prevent any residual heat from altering its properties. Subsequently, the charcoal is transferred to suitable storage containers, such as airtight bags or containers, to maintain its quality and prevent moisture absorption. Finally, the kiln is cleaned thoroughly to prepare it for the next batch, ensuring optimal conditions for the carbonization process.
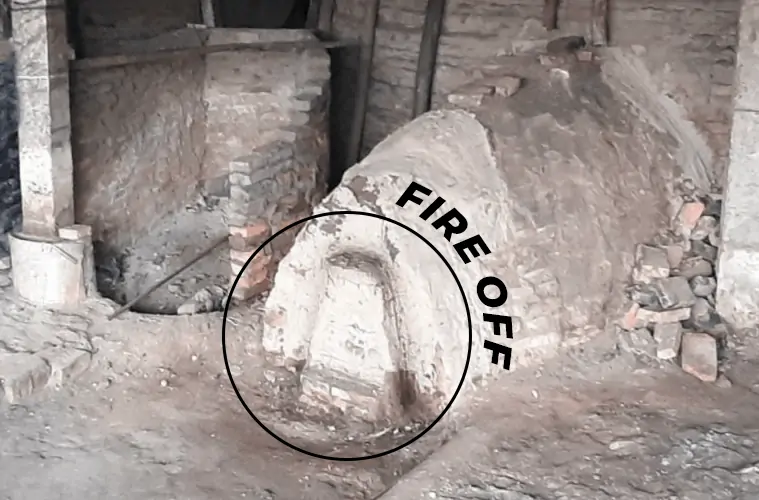
Step 5 – Open the kiln and take out the charcoal
First, the kiln needs to be cooled down to a safe temperature to prevent any potential hazards. Then, the cover or sealing material is removed carefully to reveal the charcoal inside.
Visual inspection is conducted to ensure that the charcoal has undergone proper carbonization, displaying a uniform black color and firm texture. Using appropriate tools, such as shovels or tongs, the charcoal is delicately removed from the kiln, avoiding any damage. Once extracted, the charcoal is allowed to cool further outside the kiln to prevent any residual heat from affecting its quality.
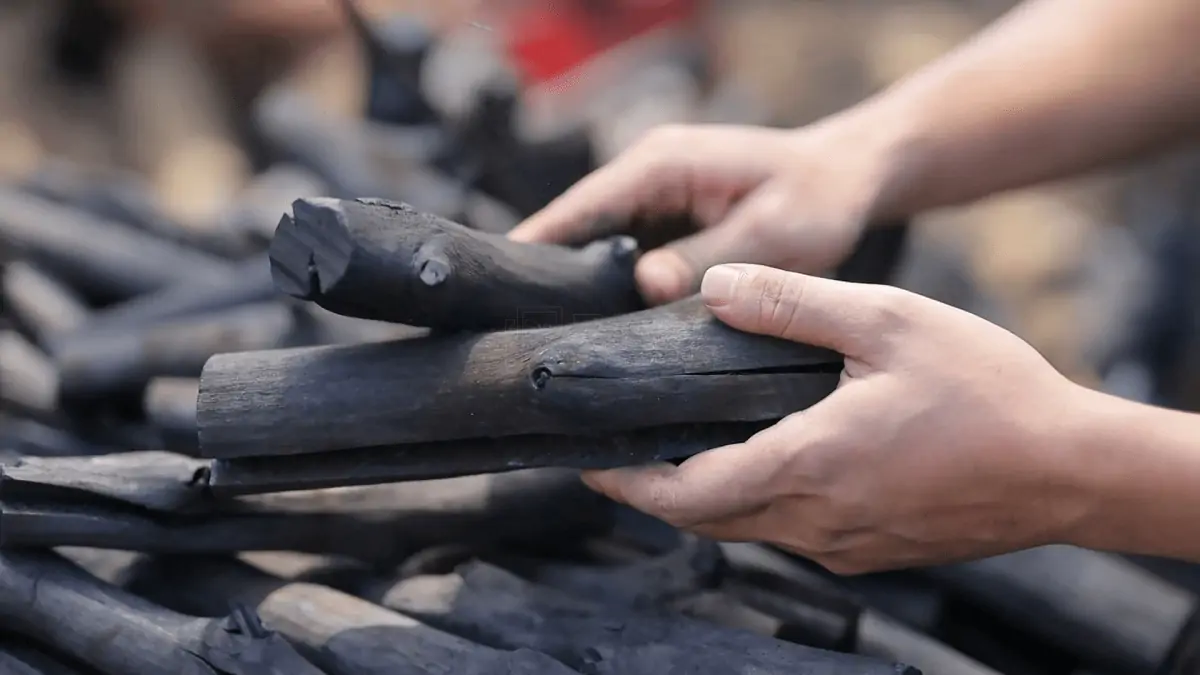
Step 6 – Leave the Charcoal Cooldown Naturally
\Finishing the carbonization process and let the charcoal cool itself in 15-20 days. While waiting for the coal to cool, we will check other steps such as the heating process of another coal pile or the storage process while the coal cools.
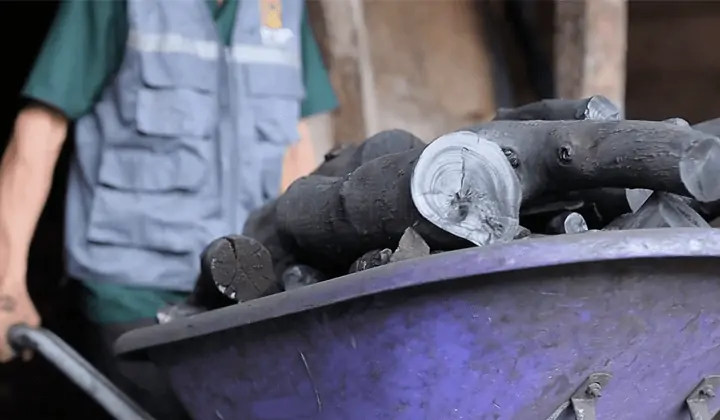
Step 7 – Classifying coal quality
In the charcoal production process, ensuring quality can be as simple as visually inspecting the charcoal and listening for any signs of poor quality. If a piece of charcoal appears brown in color or emits a sound that doesn’t meet the expected quality standards, it can be removed manually from the production line
Experienced professionals in this field easily distinguish good or bad coal quality with utmost accuracy. When cutting charcoal to the standard size, it emits a characteristic sound :
Good quality charcoal typically produces a clear, ringing sound when tapped together. This sound indicates that the charcoal is dense and well-processed, with uniform composition and minimal impurities. It resonates with a consistent tone, signifying solidity and integrity.
On the other hand, lower quality charcoal may produce a dull thud or a crackling noise when tapped. This sound suggests that the charcoal is less dense and may contain irregularities or pockets of air, compromising its overall quality and burning efficiency. It lacks the crispness and clarity of sound characteristic of high-quality charcoal.
In summary, the difference in sound between good and poor quality charcoal lies in the clarity, resonance, and consistency of the tone produced when the charcoal pieces are taped together.
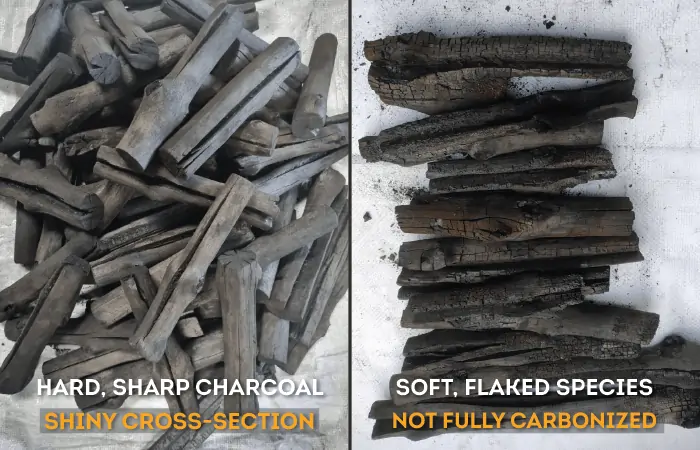
Step 8 – Cut the charcoal into the required size
After choosing good and quality charcoal, our PNP employees will move them into a cut machine to adjust based on customer demand.
Throughout the cutting process, quality control measures are implemented to monitor the size and consistency of the cut charcoal pieces. Any deviations from the desired size parameters are identified, and adjustments may be made to the cutting equipment as needed.
After cutting, the charcoal pieces are typically packaged immediately to preserve their quality and prevent moisture absorption. Packaging can range from bags to bulk containers depending on the intended use and market requirements. Finally, the packaged charcoal is stored in a dry, ventilated area ready for distribution.
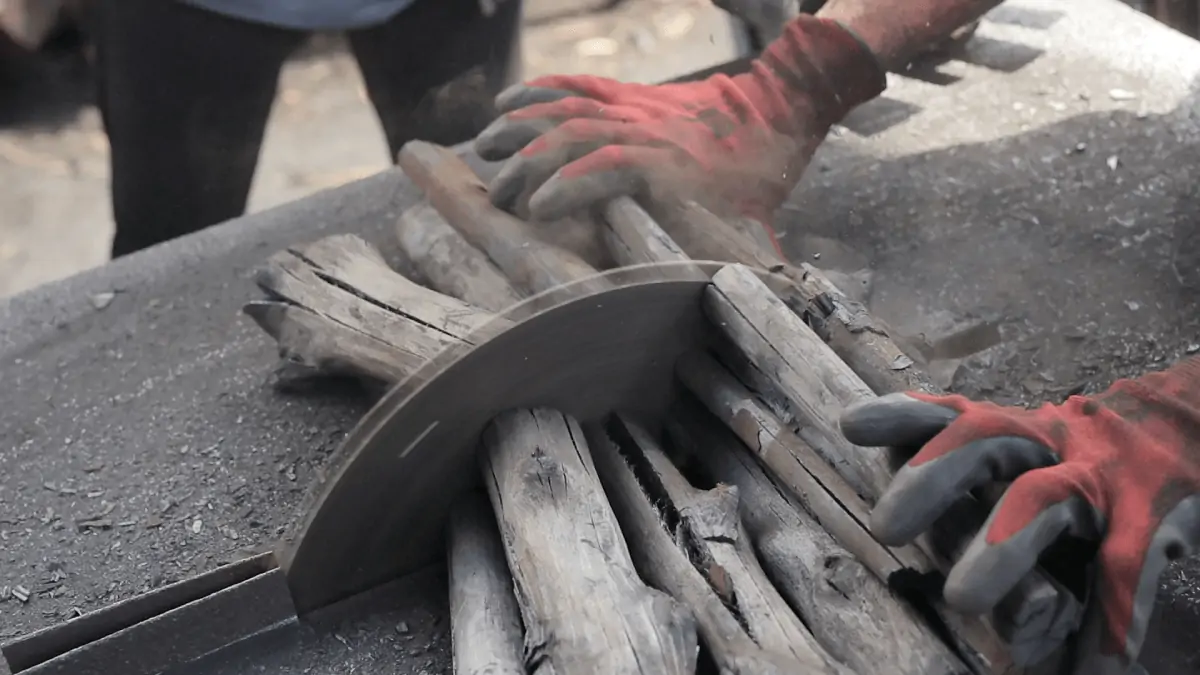
Step 9 – Store the charcoal in a cool and dry place
Charcoal should be stored in a cool, dry place to prevent moisture absorption, which can affect its burning efficiency and quality. Facilities should be equipped with proper ventilation to prevent humidity buildup, and storage areas should be protected from direct sunlight and rain
Additionally, charcoal should be stored away from sources of ignition or combustible materials to reduce fire hazards. So that PNP regularly inspects of storage areas to detect and address any issues that may compromise the quality of stored charcoal.
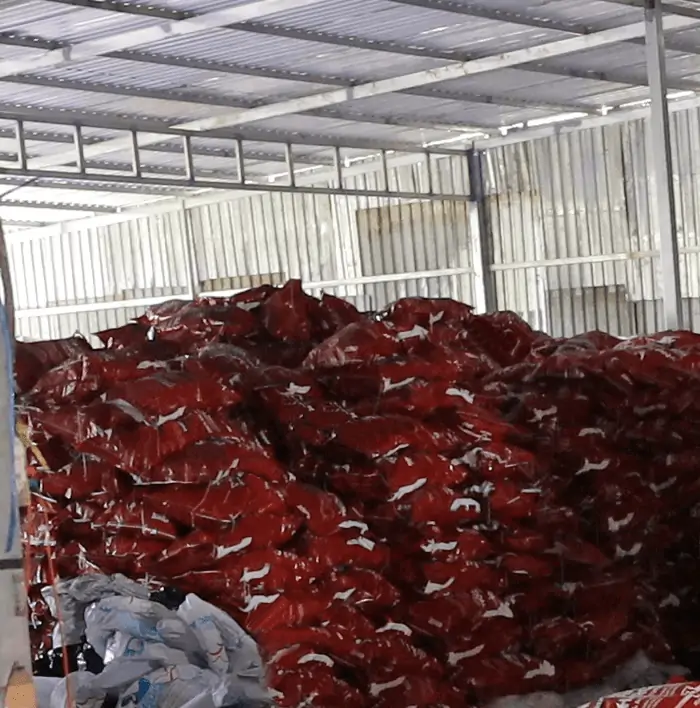
Step 10 – Test the temperature of the charcoal and inside the container
PNP employees will use perature monitoring devices such as thermometers or infrared temperature guns to periodically test the temperature of both the charcoal and inside the storage containers,which helps ensure that the charcoal stored under optimal conditions to maintain its quality and prevent safety hazards.
Tem temperatures should be regularly checked and recorded, especially during hot weather or in areas prone to temperature fluctuations. If temperatures exceed recommended levels, corrective actions such as improving ventilation or relocating storage containers may be necessary to mitigate risks of combustion or spoilage.
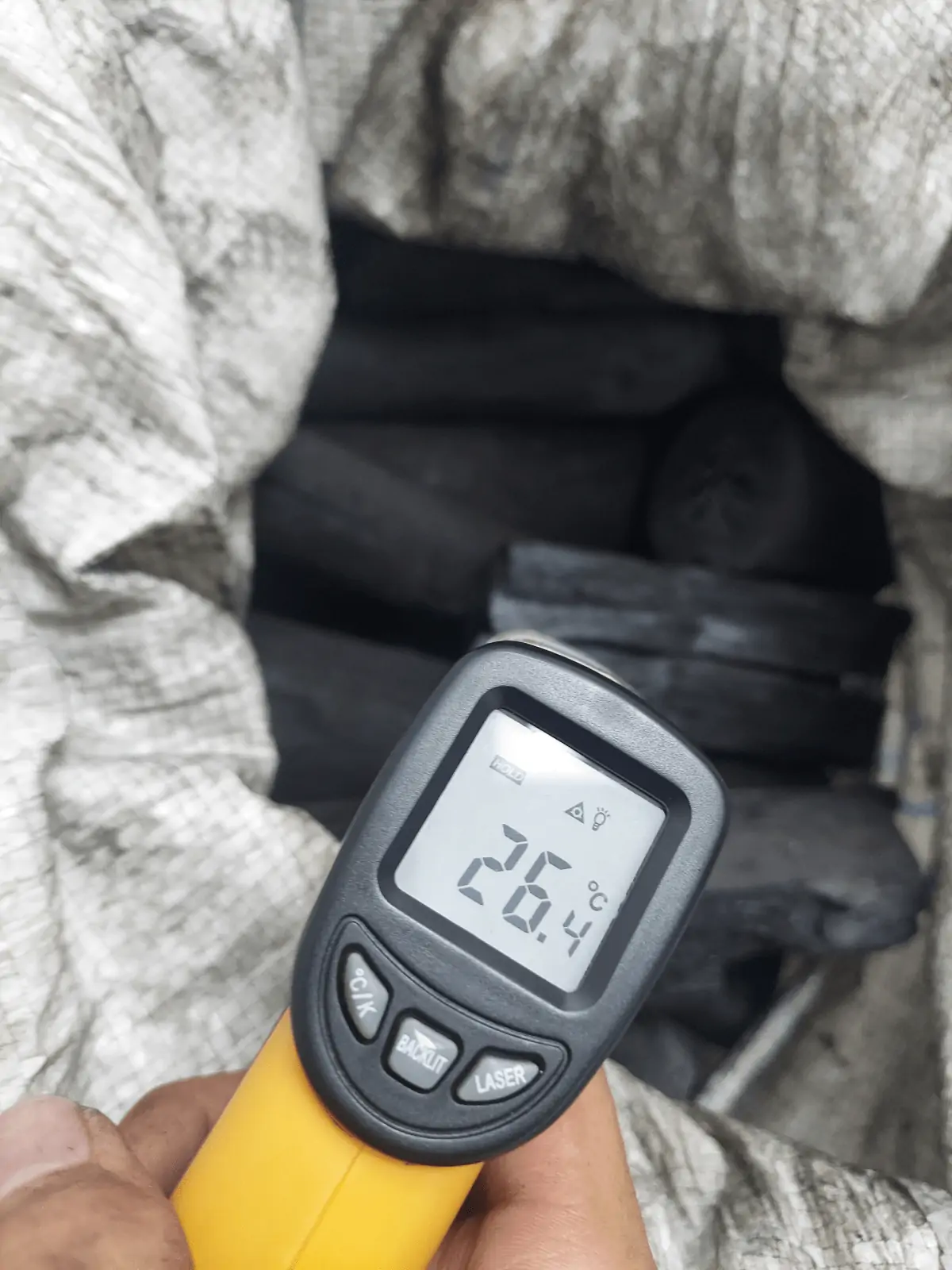
Step 11 – Arrange the charcoal into the container and deliver
After the above steps, after packing and checking the safety of the order, we will come to the final step – Vanning and shipping.
Next, PNP’ll carefully load the charcoal into the designated container, ensuring it’s securely packed to prevent spills or damage during transportation. Once loaded, we’ll organize the delivery logistics, considering factors like distance, mode of transport, and any special handling requirements. Throughout the process, PNP’ll follow safety protocols to minimize risks associated with handling charcoal.
Once the product is ready for delivery, we’ll communicate with customers promptly, providing updates on their order status and expected delivery times. Throughout this process, we’ll also be available to address any questions or concerns customers may have, providing exceptional customer service to ensure a positive experience and build long-lasting relationships.
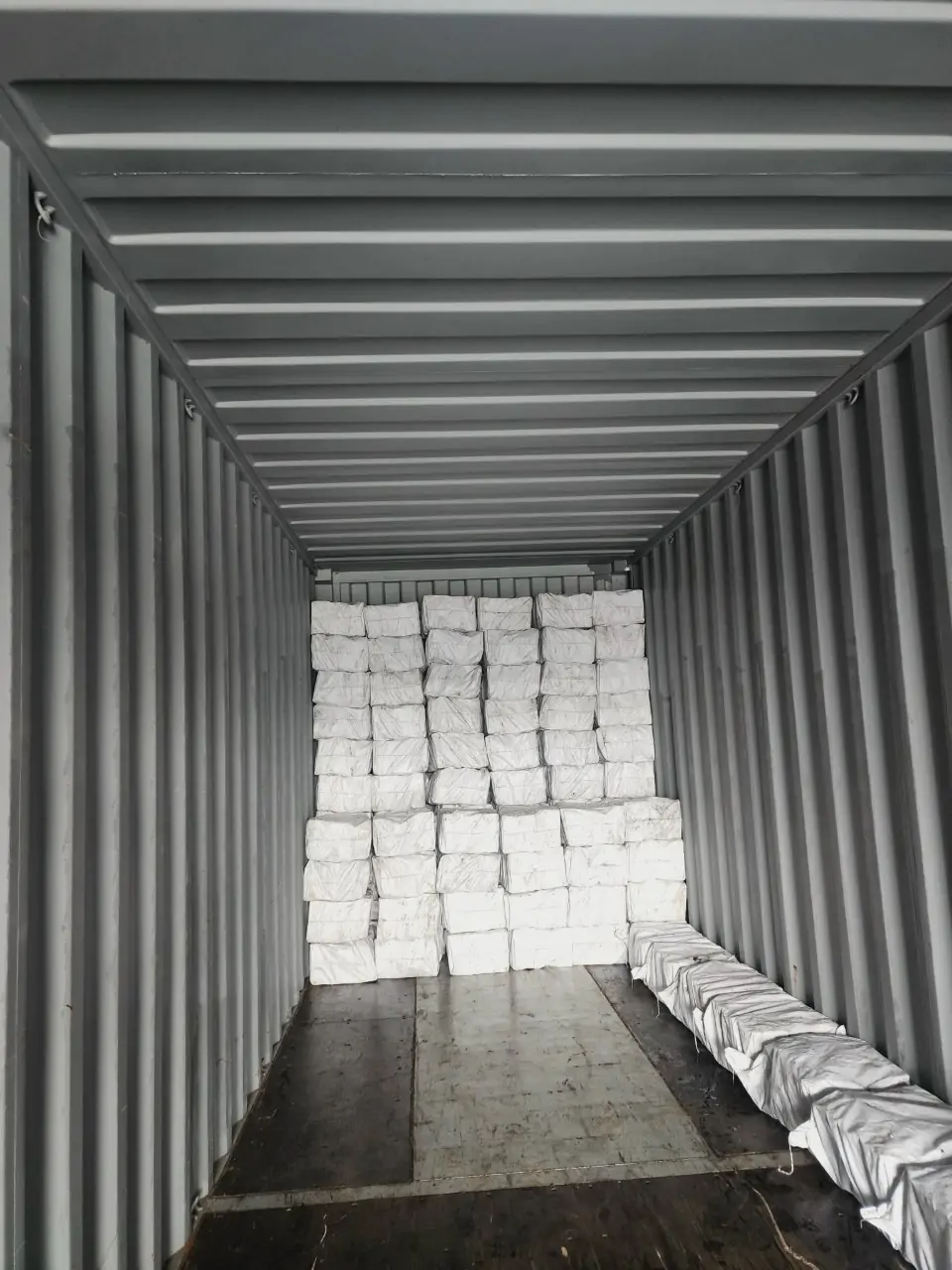
Conclusion
In general, ensuring customer satisfaction and care is a vital aspect of the charcoal production process. By conducting thorough quality checks, careful packaging, clear communication, and responsive customer service, PNP can guarantee that customers receive a high-quality product and a positive experience. This not only builds trust and loyalty but also reinforces our commitment to delivering excellence in every aspect of our operations. Ultimately, prioritizing customer satisfaction strengthens our brand reputation and sets the foundation for long-term success in the charcoal industry.
________________________________
Contact us for more information
Facebook: PNP Charcoal
Instagram: PNP Charcoal
Email: info@pnpglobalsupply.com