With rising global demand for clean-burning, long-lasting charcoal, many manufacturers are looking to upgrade their charcoal making process to meet strict export standards. From raw material selection to carbonization and packaging, every step plays a vital role in determining whether the final product is suitable for international markets.
In this article, we’ll walk you through the complete process of making charcoal, focusing on best practices for consistent quality, efficiency, and compliance with export regulations.
1. Why a Standardized Charcoal Making Process Matters
Charcoal production for export is more than just burning wood. Countries importing charcoal—especially in Europe, the Middle East, and Asia—set high requirements for moisture content, ash percentage, calorific value, and sustainability. Without a standardized charcoal making process, it’s difficult to ensure consistent product quality across batches.
Export-grade charcoal must not only perform well in terms of heat and burn time but also comply with environmental and traceability standards. This makes investing in a professional, well-documented manufacturing process a must for any serious exporter.
Global Trends in Charcoal Production
The global charcoal manufacture industry is evolving rapidly. Developing countries in Southeast Asia, Africa, and South America have become key suppliers of lump charcoal and briquettes. However, with competition growing, quality control is a major differentiator.
To meet these demands, many producers are shifting from traditional kilns to modern systems equipped with charcoal production machines, which improve consistency, reduce emissions, and increase output. These machines are changing how businesses approach charcoal making at scale.
Raw Materials Used in Wood Charcoal Making
The foundation of high-quality wood charcoal making lies in raw material selection. Common sources include:
- Hardwood species such as eucalyptus, longan, lychee, or acacia. These produce dense charcoal with high heat value and low ash.
- Coconut shells or sawdust: Ideal for compressed charcoal or biochar.
- Agricultural by-products: Sustainable alternatives for eco-conscious markets.
Raw materials must be clean, dry, and free from chemicals. Moist or contaminated wood leads to poor combustion and excessive smoke—both red flags in international charcoal production standards.

The Standard Process of Making Charcoal
A professional charcoal making process typically includes four main stages:
Step 1: Pre-processing the Material
Logs or raw biomass are cut to uniform sizes. For some applications, the bark may be removed to improve carbonization efficiency.
Step 2: Drying the Wood
Moisture content must be reduced to below 20% before carbonization. Drying can be done naturally (sun drying) or via a controlled environment (drying kilns).
Step 3: Carbonization
This is the most critical stage in the process of making charcoal. The dried material is placed into sealed kilns—either traditional earth kilns or modern retort systems—and heated between 400°C and 700°C in low-oxygen conditions.
The goal is to drive off volatile compounds while preserving fixed carbon. Depending on the system, this stage may last from 8 to 36 hours.
Step 4: Cooling and Sorting
Charcoal must be cooled gradually to avoid spontaneous combustion. Once fully cooled, the product is sorted by size, tested for quality, and packed into moisture-resistant bags for export.
A well-structured charcoal manufacture process ensures higher yields, stronger charcoal, and improved burn performance.
Learn more about different methods of charcoal production through the following article: what are the different types of charcoal production
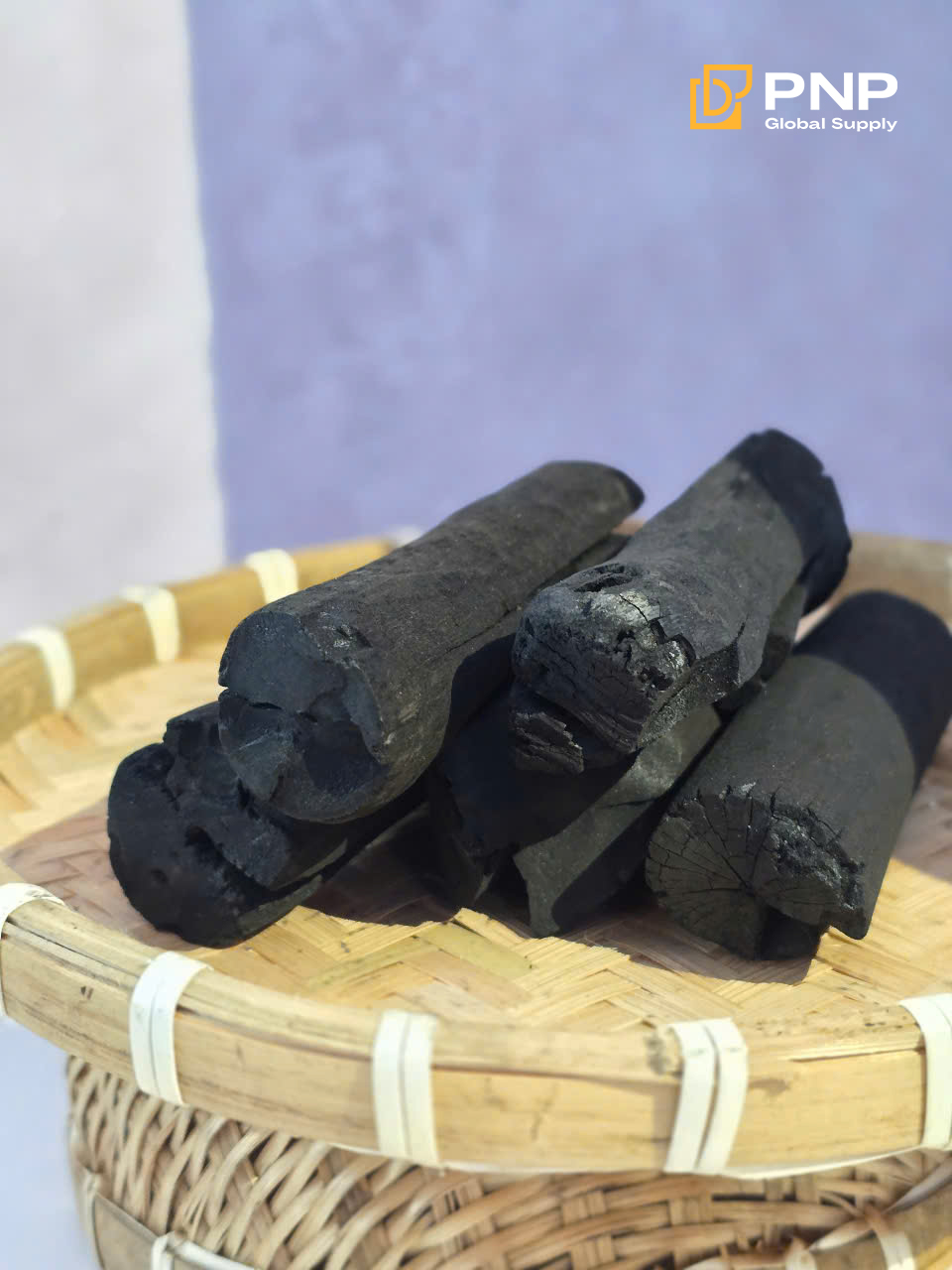
The Role of Charcoal Production Machines
Modern charcoal production machines are revolutionizing the industry by offering efficiency, consistency, and environmental control. Common equipment includes:
- Drying systems: Accelerate the removal of moisture from raw materials.
- Continuous carbonization kilns: Automate temperature control and airflow, improving carbonization efficiency and reducing emissions.
- Conveyor belts and packaging units: Streamline sorting, cooling, and bagging.
Switching to a mechanized system reduces labor costs, boosts production volume, and ensures that each batch of charcoal meets export-grade specifications.
Key Quality Standards for Export Charcoal
To qualify for international markets, your charcoal must meet several benchmarks:
- Fixed Carbon: Above 65%
- Ash Content: Below 7%
- Moisture Content: Below 5%
- Calorific Value: Over 6500 kcal/kg
- Burning Time: Minimum 2.5 hours (depending on type)
- Odor-Free, Spark-Free, No Chemical Additives
Manufacturers who follow a standardized charcoal making method and regularly test their output are more likely to meet these strict quality requirements. Certification from third-party labs can further boost buyer confidence.
PNP Charcoal offers a wide range of high-quality charcoal to meet various needs. Learn more about our charcoal products here: pnpcharcoal
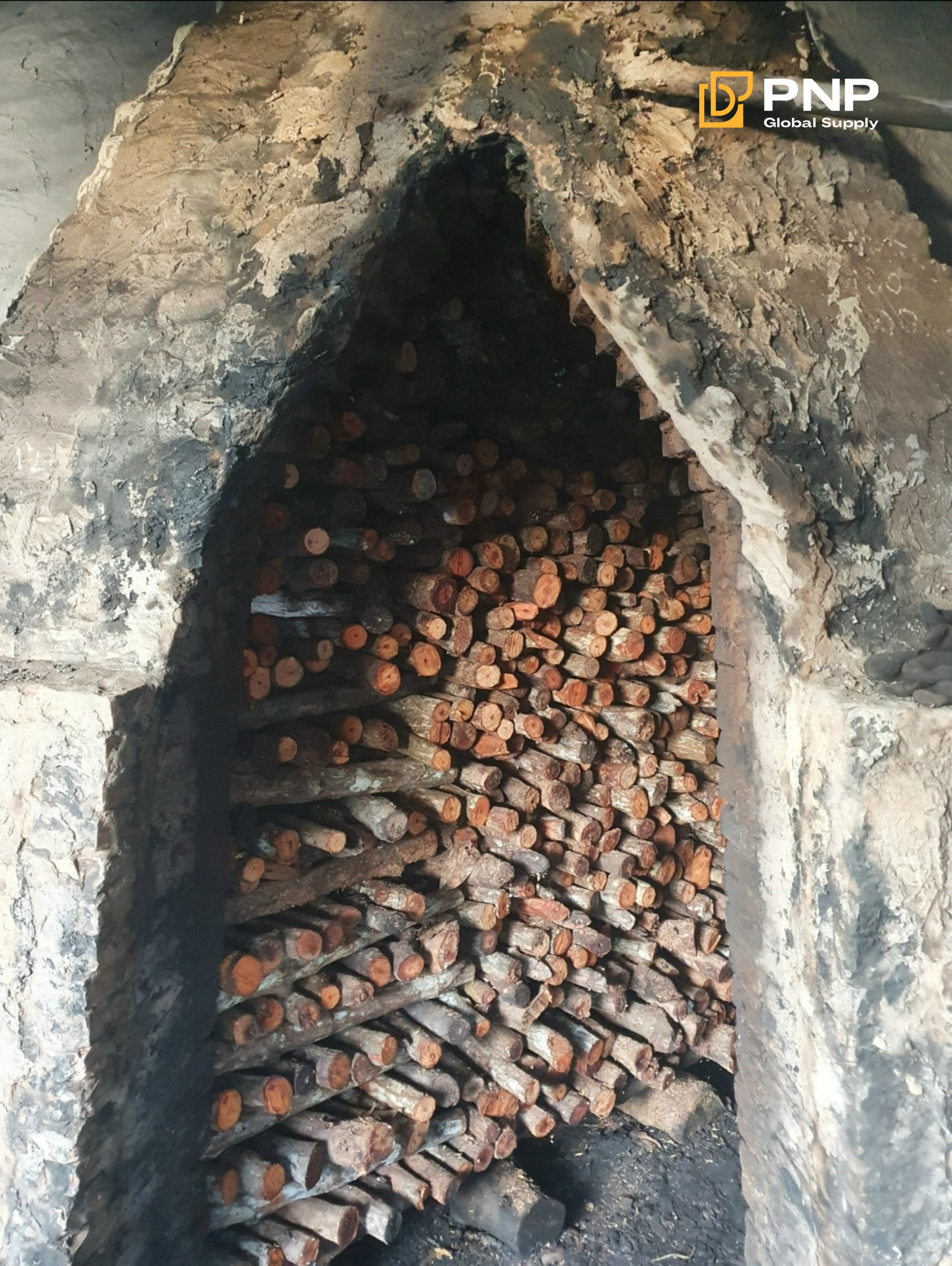
Challenges in Manufacturing Charcoal for Export
Even with a solid charcoal manufacture plan, producers face several challenges:
- Raw Material Supply: Deforestation laws and seasonal shortages can disrupt production.
- High Equipment Costs: Modern kilns and dryers require significant capital investment.
- Emission Control: Non-compliant kilns may face regulatory penalties for air pollution.
- Labor Skills: Improper handling of kilns or poor sorting can result in substandard products.
Despite these issues, forward-looking businesses are overcoming obstacles through innovation, automation, and training. Those who invest in clean charcoal production systems are more likely to succeed long-term.
Conclusion
Success in the export charcoal business doesn’t happen by chance. It begins with a consistent, well-documented, and optimized charcoal making process. From selecting the right wood to using the right machinery and maintaining high quality standards, every step must align with international expectations.
Whether you’re looking to improve your charcoal production for local or overseas markets, upgrading your processes is the best investment you can make.
________________________________
Contact us for more information
Facebook: PNP Charcoal
Instagram: PNP Charcoal
Email: info@pnpglobalsupply.com