Charcoal kilns are important coal production equipment, helping transform raw materials into final products. However, users often encounter problems such as low performance, unstable product quality and high fuel consumption. This article will help you understand the influencing factors and provide tips for optimizing your charcoal kilns.
Understand the charcoal kiln heating process
Operating principle:
Charcoal kilns operate based on the pyrolysis principle – the process of decomposing wood into charcoal, gas and water when burned in oxygen-deficient conditions. The wood is placed in the furnace, sealed and partially burned to create high temperatures. Under the influence of heat, wood decomposes, releasing gases and leaving the solid part, charcoal. This process requires strict control of temperature and oxygen levels to ensure charcoal quality. Wood type, temperature, firing time and kiln design all affect the efficiency of this process. The obtained charcoal has many applications in life and production thanks to its high energy and environmental friendliness.
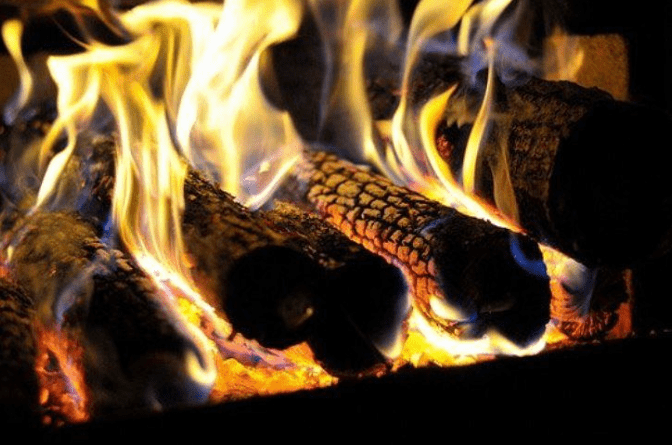
Factors affecting the performance of Charcoal kilns
Through detailed research, many factors determine the effectiveness of the charcoal firing process, including the type of wood used, the moisture content of the wood before burning, the ideal temperature that the charcoal kilns needs to achieve, and the amount of Oxygen is present during the process, as well as the time it takes to burn the wood.
- Choosing the right type of wood is very important, because each type of wood will have a different chemical composition, directly affecting the quality of the charcoal obtained. At the same time, the moisture content of wood is also a factor that cannot be overlooked; Wood that is too damp will make the firing process difficult and reduce efficiency.
- The amount of oxygen in the furnace also needs to be strictly controlled, because too much oxygen can lead to complete combustion, while a lack of oxygen reduces coal quality and creates toxic gases.
- Firing time also plays an important role, because if this process lasts too long or too short, optimal results will not be achieved.
Popular types of charcoal kilns
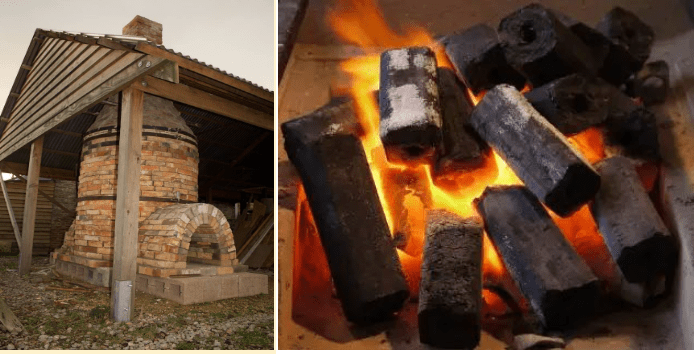
- Traditional charcoal kilns: This is a simple furnace, usually made from soil or bricks. This furnace uses wood materials to produce charcoal, often used in rural areas.
- Industrial charcoal kilns: This type of furnace is designed to produce coal on a larger scale. They are typically made of steel and have better temperature control, helping to produce higher quality coal.
- Gasification charcoal kilns: This is a modern furnace, using gasification technology to convert raw materials into gas and then into coal. This furnace is highly efficient and causes less pollution than traditional furnaces.
- Electric charcoal kilns: Using electricity to generate heat, this type of furnace is often used in industrial applications and has precise temperature control.
Tips for optimizing charcoal kilns
Charcoal kilns optimization is essential to improve production efficiency, reduce carbon emissions and improve the overall quality of coal. By implementing effective strategies, manufacturers can not only increase production but also contribute to more sustainable practices in the charcoal industry. Here are some valuable tips for optimizing your charcoal kilns.
Using advanced kiln designs
One of the most effective ways to optimize coal production is to use advanced kiln designs. Modern furnaces incorporating methane recycling technology can significantly reduce carbonization time. Traditional kilns can take up to 7 days to produce coal, but with advanced designs, this time can be reduced to just 72 hours. This reduction not only speeds up the production cycle but also reduces emissions, making the process more environmentally friendly.
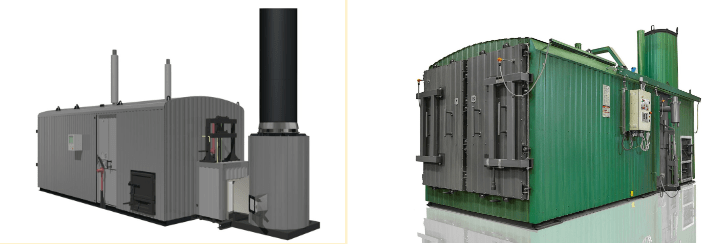
Improve fuel efficiency
Another important aspect of charcoal kilns optimization is testing alternative fuels. Using materials such as wood chips, briquettes and pellets can improve combustion efficiency. These alternatives can reduce the amount of raw wood needed for production, leading to a more sustainable approach. By improving fuel efficiency, manufacturers can reduce costs and minimize environmental impact.
Optimized loading technique
Proper loading technique is important to maximize airflow and heat distribution within the furnace. Strategically arranging the wood allows for optimal air circulation, which can lead to more uniform carbonization. This approach not only improves the quality of coal produced but also enhances the overall efficiency of the furnace. Ensuring wood is loaded properly can make a significant difference to the final product.
Control temperature and air flow
Maintaining proper temperature and air flow in the furnace is critical for successful carbonization. Monitoring these factors allows the manufacturer to create ideal process conditions, prevent incomplete combustion and improve coal yield. By regularly adjusting temperature and airflow, operators can ensure the furnace is operating at peak efficiency, delivering higher quality coal.
Regular maintenance
Regular furnace maintenance is essential for optimal performance. Keeping the furnace clean and well-maintained will help avoid airflow blockages and ensure that all parts operate correctly. This proactive approach can prevent inefficiencies and extend the life of the furnace. Regular inspection and maintenance are key to maintaining high production levels.
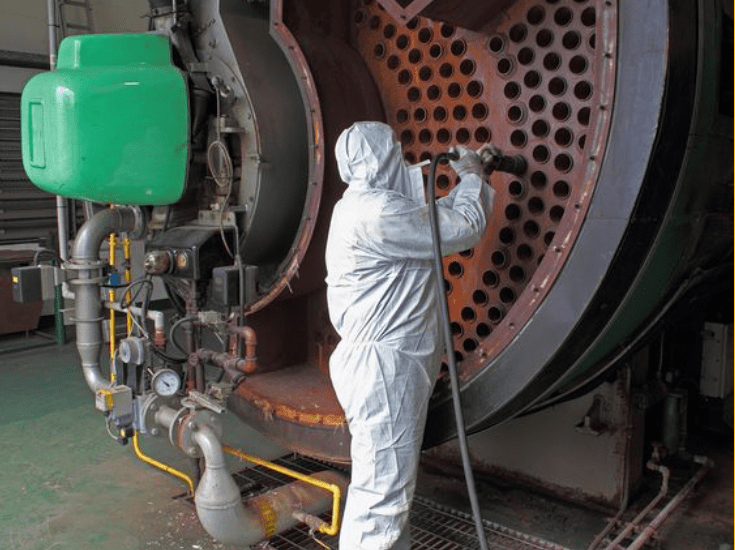
Monitor the carbonization process
The use of temperature sensors and monitoring tools can significantly enhance the carbonization process. By monitoring conditions in the furnace, operators can make real-time adjustments to improve efficiency and product quality. This data-driven approach allows for more precise control of the carbonization process, delivering better results.
Experiment with different types of wood
Different types of wood produce different qualities of charcoal. By testing many different types of wood, manufacturers can determine the best options for their specific needs. This test can help improve coal quality and better marketability. Understanding the properties of different types of wood can help choose the most suitable material for production
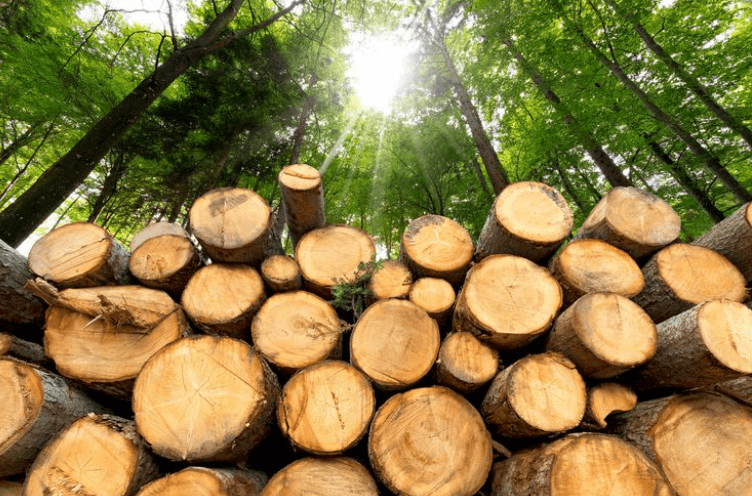
Benefits of charcoal kilns optimization
Charcoal kilns optimization brings many important benefits to the coal mining and production industry, not only bringing economic benefits but also contributing to the sustainable development of the coal industry.
- First, charcoal kilns optimization helps increase coal output and quality, ensuring that the final product meets market demands and high quality standards.
- Second, charcoal kilns optimization also helps reduce production costs and environmental impact. By improving production processes, businesses can save energy and raw materials, thereby reducing emissions and waste into the environment.
- Ultimately, charcoal kilns optimization also creates safer and cleaner coal products for consumers, contributing to protecting public health and enhancing brand reputation in the industry.
Conclusion
By implementing coal kiln optimization measures, coal producers can significantly enhance the performance of their kilns. From using advanced designs and improving fuel efficiency to optimizing charging techniques and maintaining proper temperature control, every step contributes to better quality coal and more sustainable production practices. Applying these tips not only benefits manufacturers but also supports environmental sustainability in the charcoal industry. As demand for coal continues to increase, optimizing production methods will be important to meet market demand while minimizing ecological impact.
________________________________
Contact us for more information
Facebook: PNP Charcoal
Instagram: PNP Charcoal
Email: info@pnpglobalsupply.com